I swear the demand most people make of me is to 'be patient'. Be patient with healing. Be patient with grief. Be patient about the Land Rover Defender 130 pop top build your husband is constructing.
I am not good at patience.
But as the other pithy saying goes, 'good things take time'. And damn, this is a good thing. Having a vehicle like this is damn epic. We haven't got there the easy way. It's been years in the making - we bought it cheap in 2020, and Jamie's worked hard to rebuild it, paint it, fit it out, kit it out, and now pop it.
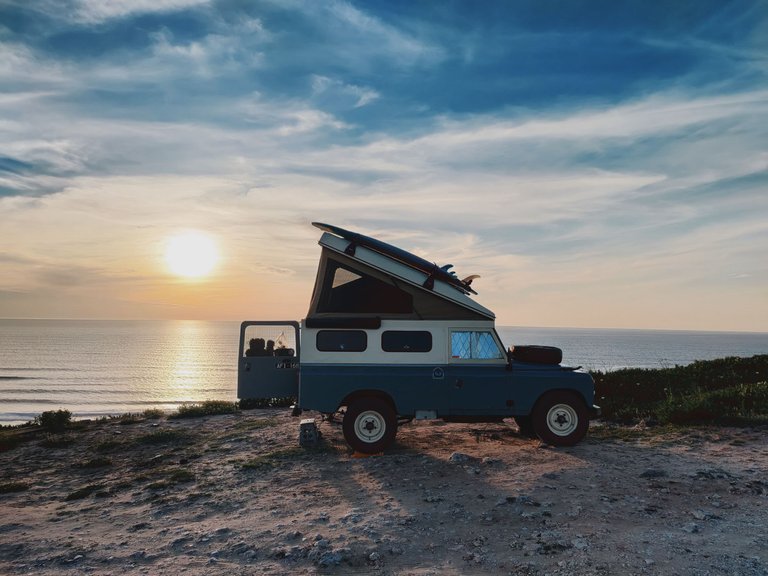
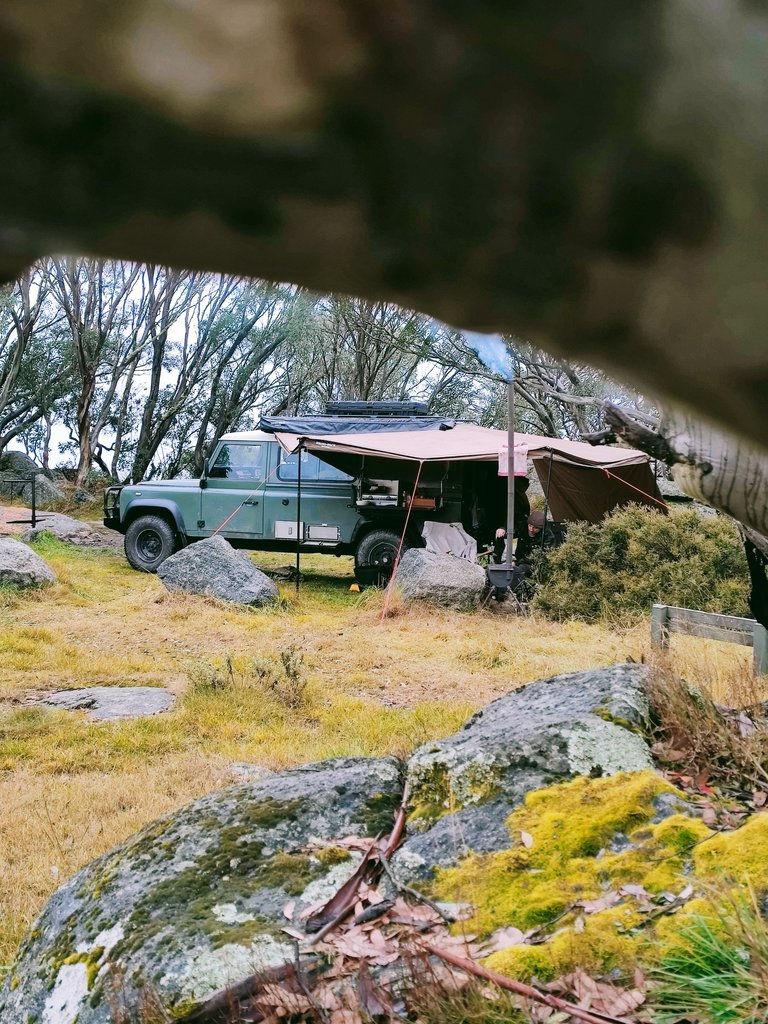
After travelling with our pop top Land Rover Series 3 early in the year (also self build) we decided we absolutely had to do it again to the 130. If you don't know about Land Rovers, the 130 is the wheel base - most of them are 110, so it's a bit longer. That gives us a lot of extra space.
Here you can see the roof off and the bottom half of the clam shell rested on top of the panelvan. Jamie spent a day strengthening the body to take the extra weight, which will be good when we get an engineer to sign off on it.
We are so lucky that we have the engineering expertise of Murray, who has a Land Rover accessories business. He's been brainstorming with Jamie and engineering the pop top as he may well sell them as build your own kits. This will bring them down in price - a lot. Usually an Alucab pop top will be around 20k AUD. Ours won't be anything near that amount, and less as it's a prototype build together with Murray so we will only be paying for materials.
Today the two of them are reconstructing the roof. Then it will go off to the powder coaters and in a weeks time hopefully will be attached and we can go to the canvas people so they can sew that up. THEN we will get down to rebuilding the cabinetry and making the bed!
As the roof is made from a 110 and a 130 roof, it was a little patchwork, and because Murray had come up with a better way to make the back of the pop top roof look streamlined and professional, they decided they were going to make the roof even better. This meant getting a whole sheet of aluminium and bending it, and making bespoke guttering as well. As I write they're in their second day of building the thing so they can mock fit it to the clamshell top to put riv nuts in before it goes to powder coaters. Waht a mission. Lucky Murray has the machinery to do it!
To make the curve of the roof, Murray must have made about twenty folds at least. He's also made us some cool bespoke latches that'll go on the back to hold it down as well. It's going to be so epic!
I probably should make Jamie a sandwich and take it over to him where he's working - poor guy hasn't stopped in months. It'll be worth it though, don't you think?
With Love,
Are you on HIVE yet? Earn for writing! Referral link for FREE account here